Significado de Acero | Sinónimos y oraciones con ejemplos de uso de Acero
Significado de «Acero (aleación férrica)»
El acero es una aleación férrica que combina hierro con cantidades reducidas de carbono, manganeso, fósforo, azufre y silicio.
Además de estos elementos, las aleaciones aceradas pueden incluir níquel, cromo, molibdeno, vanadio, tungsteno, cobalto, selenio, columbio, titanio, boro, circonio y aluminio.
Esta composición le confiere al acero propiedades únicas que lo han convertido en un material fundamental en la industria y la construcción.
La historia del acero se remonta a siglos atrás, siendo un material clave en el desarrollo de la humanidad.
Tabla de contenido
Definición de Acero
Autor: Leandro Alegsa
Número de letras: 5
Posee un total de 3 vocales: A e o
Y un total de 2 consonantes: c r
¿Preguntas sobre el significado de esta palabra?: respondemos aquí
[ Imágenes relacionadas a "Acero" ]
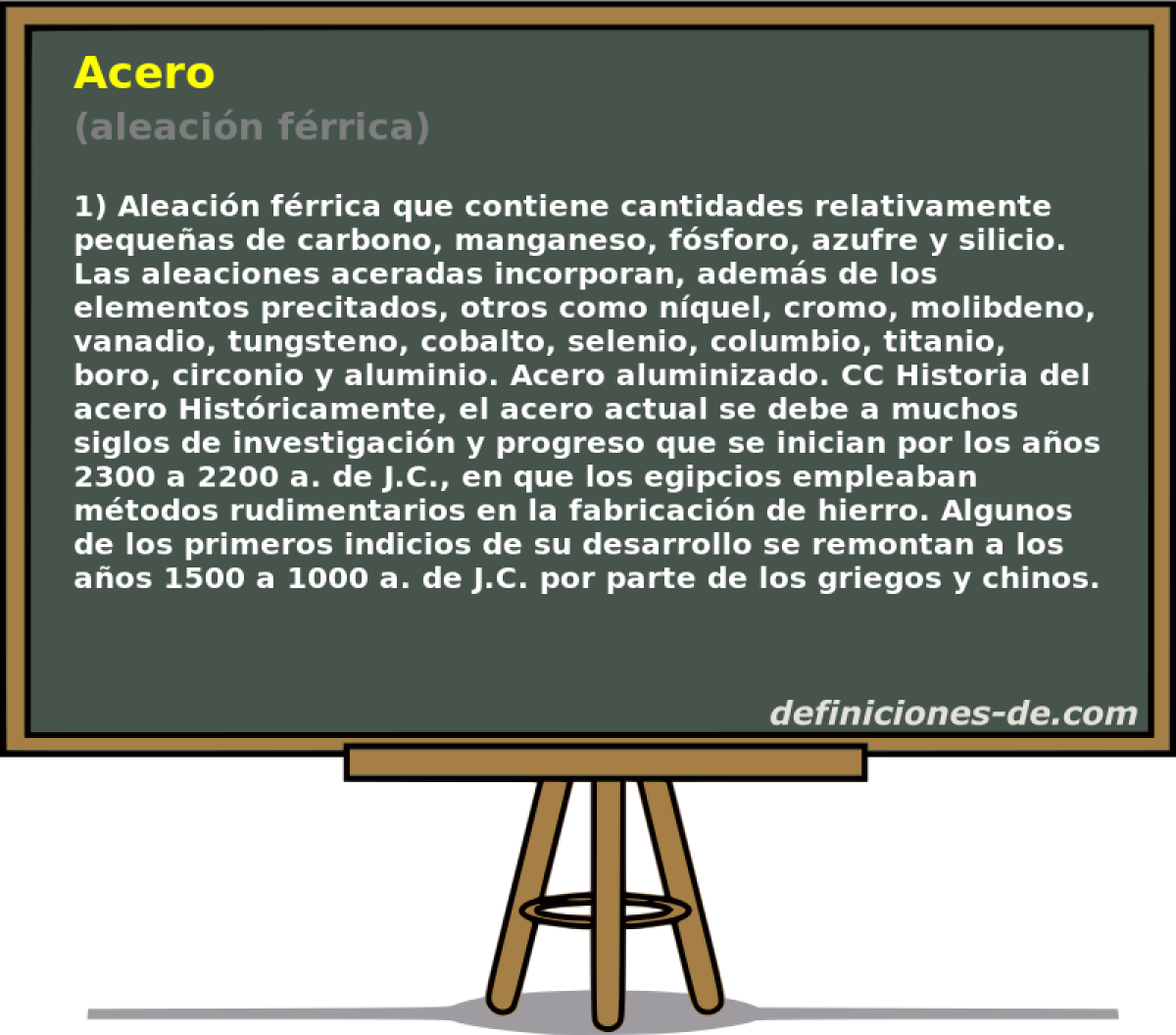
Esta imagen puedes emplearla con fines didácticos en la escuela, institución educativa o proyectos web.
Además de estos elementos, las aleaciones aceradas pueden incluir níquel, cromo, molibdeno, vanadio, tungsteno, cobalto, selenio, columbio, titanio, boro, circonio y aluminio.
Esta composición le confiere al acero propiedades únicas que lo han convertido en un material fundamental en la industria y la construcción.
La historia del acero se remonta a siglos atrás, siendo un material clave en el desarrollo de la humanidad.
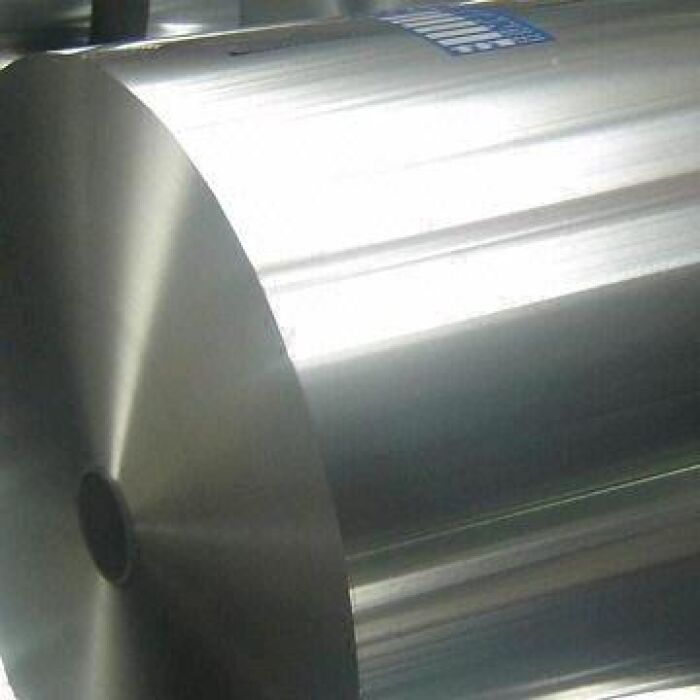
Definición de Acero
- Aleación férrica que contiene cantidades relativamente pequeñas de carbono, manganeso, fósforo, azufre y silicio. Las aleaciones aceradas incorporan, además de los elementos precitados, otros como níquel, cromo, molibdeno, vanadio, tungsteno, cobalto, selenio, columbio, titanio, boro, circonio y aluminio.
Historia del acero
Históricamente, el acero actual se debe a muchos siglos de investigación y progreso que se inician por los años 2300 a 2200 a. de J.C., en que los egipcios empleaban métodos rudimentarios en la fabricación de hierro. Algunos de los primeros indicios de su desarrollo se remontan a los años 1500 a 1000 a. de J.C. por parte de los griegos y chinos. El progreso real fue lento hasta que Huntsman, por el 1740, inventó el procedimiento del crisol, al que siguió, en 1855, el de Henry Bessemer. Desde entonces, la industria del acero ha contribuido considerablemente al desarrollo de las industrias transformadoras tal como hoy las conocemos. La introducción del horno de reverbero Martin-Siemens en 1864 y su adopción por la industria han movilizado las inmensas posibilidades del acero. La necesidad de disponer de aceros de mejor calidad originó el descubrimiento del horno eléctrico por Heroult en 1890. Los aceros modernos se clasifican en aceros ordinarios al carbono, aceros aleados y aceros inoxidables. Los primeros se producen generalmente mediante el proceso Bessemer o de reverbero mientras que los dos restantes se obtienen en los procesos de horno de reverbero y eléctrico. Sólo se emplea el proceso de crisol en la fabricación de aceros especiales aleados para herramientas.
Procesos de producción de acero
El de Bessemer consiste en insuflar aire a la fundición líquida contenida en un horno basculante piriforme. El carbono, silicio y manganeso se reducen por oxidación. Los aceros Bessemer se denominan de proceso ácido o básico según que el revestimiento refractario del convertidor sea silíceo o magnésico. La colada media oscila entre las 25 y 30 toneladas.
En el proceso del crisol se funden barras de hierro pudelado con carbón vegetal y arena dentro de un crisol carbonado. El hierro se refina, cementa y se vierte en lingoteras. Las cargas suelen ser de 30 a 45 kilogramos.
Las acerías obtienen la mayor parte de su producción mediante el procedimiento de reverbero y producen aceros básicos o ácidos según el método de afino. El proceso básico es, sin duda, el más aceptado, ya que permite la reducción del fósforo, carbono, azufre, manganeso y los restantes elementos. La carga de chatarra y de lingote o de lingote solamente, fundida en el proceso básico principalmente en piedra caliza y espato flúor, se refina en un horno de reverbero calentado por aire a presión y gas o petróleo combustible. Después de la operación de afino necesaria para eliminar impurezas, el acero es desoxidado y vertido en un cucharón, de donde pasa alas lingoteras. Las coladas obtenidas por este proceso oscilan entre 100 y 200 toneladas.
Los hornos eléctricos, ya sean de arco eléctrico o de inducción, aventajan a cualquier otro proceso de fabricación de acero al utilizar la energía eléctrica para el caldeo. Una gran ventaja es la obtención de temperaturas más elevadas con un coste menor, pero mayor importancia tiene la posibilidad de regular el aire y refinado de la escoria con mayor precisión, puesto que el operario puede trabajar a voluntad la carga de chatarra y de acero fundido o sólo de acero en un horno de reverbero en condiciones primero de oxidación y luego de reducción. Las impurezas, por tanto, quedan reducidas ai mínimo y el acero obtenido es de calidad inmejorable.
El término «proceso dúplex» implica el refino preliminar de una colada mediante un proceso al que sigue otro refino posterior por proceso diferente. Al principio se refería únicamente a! soplado del metal en los convertidores Bessemer que era seguido por la refinación realizada en los hornos de solera abierta o reverbero.
En el procedimiento de «colada continua», la fabricación de lingotes se reduce a una sola operación y se abrevia el «blooming». V. Colada continua.
Elementos de la aceración del acero
Para comprender mejor las características del acero es necesario conocer las funciones de sus componentes. El carbono es su principal elemento endurecedor y se combina con el hierro para formar el compuesto llamado cementita o carburo férrico. El manganeso actúa como fuerte elemento cementador y es también desoxidante y desulfurante. El fósforo es una impureza que reduce Ía ductilidad del acero y lo hace propenso a la ruptura en los trabajos de forja. El azufre actúa de forma similar, aunque favorece las propiedades mecanizables del acero. El silicio es desoxidante y en ciertas condiciones aumenta las propiedades físicas y la permeabilidad magnética necesarias en los núcleos para transformadores y alternadores. El aluminio, el níquel, el circonio y el silicio están mezclados con la ferrita o hierro puro. El níquel, particularmente, aumenta la resistencia a ía tracción y choques del acero. El cromo, el tungsteno, el molibdeno y el vanadio están disueltos en parte en el hierro puro, pero son muy activos en la formación de carburos al combinarse con el carbono presente en el acero; dichos elementos aumentan la dureza, la resistencia a la tracción, a la abrasión y al desgaste y la capacidad de soportar temperaturas elevadas.
Los elementos actúan solos o combinados para proporcionar las propiedades deseadas. Las aleaciones son conocidas por los nombres de aceros al níquel, al cromo, al manganeso, al silicio, al molibdeno, al tungsteno y al vanadio. Muy comunes son las designaciones de acero con el 1,25 % de níquel y el 0,60 % de cromo; con el 1 % de cromo y el 0,20 % de molibdeno; con el 1,75 % de níquel y el 0,20 % de molibdeno; con el 1 % de cromo y el 0,15 % de vanadio. Los que contienen de 4 a 24 % de tungsteno como aleación principal se llaman aceros de herramientas. Durante la 1era Guerra Mundial el molibdeno substituyó al tungsteno hasta cierto punto en la fabricación de esta clase de aceros; el más corriente contenía el 6 % de ambos elementos. Las aleaciones principales de los aceros inoxidables son el níquel y el cromo. Hay dos tipos. Uno es el sencillo de acero y cromo o acero inoxidable ferrítico, que contiene de 5 a 27 % de cromo. El otro contiene, además de cromo, de 2 a 20 % de níquel; la composición común es de 18 % de cromo y 8 % de níquel. Si se emplea sólo el níquel en cantidad equivalente al 36 %, se obtienen aceros cuya dilatación térmica es muy baja; son muy valiosos en la fabricación de cintas métricas para agrimensores y en la de aparatos de medida de gran precisión.
Clasificación y aplicación de los aceros
Se clasifican en tres grupos generales: aceros ordinarios al carbono (no aleados o binarios), aceros aleados y aceros inoxidables, de acuerdo con su composición, propiedades físicas, aplicación y procesos de fabricación.
Los aceros no aleados se suelen obtener por el proceso Bessemer o de solera abierta (reverbero) y contienen principalmente carbono, manganeso, fósforo, azufre y silicio. Los aleados se caracterizan porque contienen, además de los elementos antes citados, cantidades suficientes de otro u otros aleables que modifican marcadamente sus propiedades físicas. Los inoxidables son aceros aleados, aunque se clasifican separadamente en atención a. su inoxidabilidad, que no poseen los de las otras categorías. Los aceros inoxidables y aleados de alta calidad se obtienen por el proceso del horno eléctrico, aunque el de solera abierta se usa ampliamente en la producción de aceros binarios y aleados de calidad superior.
Las aplicaciones de los aceros no aleados son muchas y variadas. Se utilizan principalmente en la construcción, en la fabricación de aparatos domésticos y máquinas agrícolas, en la industria conservera, automovilística y ferroviaria. Se emplean cuando es necesaria la aplicación de sus características: aptitud de conformación, estampado profundo, fuerza estructural y resistencia media. Ejemplos de su empleo nos los ofrecen las carrocerías de automóviles y vagones, los carriles, los bastidores para enseres domésticos y máquinas agrícolas, los recipientes, armazones de construcción, envases de hojalata y piezas galvanizadas. La elección de los tipos apropiados de aceros ordinarios para las aplicaciones mencionadas, basada en su contenido de carbono, ofrece tres grupos: acero suave con un contenido de 0,2 % aproximadamente; acero medio, con 0,20 a 0,50 %; acero alto, con más de 0,50 por ciento.
Los aceros aleados se utilizan cuando se necesitan materiales capaces de resistir cargas, desgastes, temperaturas, abrasiones y fatigas excesivas. Se utilizan, por tanto, en las industrias automovilística, aeronáutica, petrolífera, ferroviaria y de equipos pesados para la fabricación de piezas tales como engranajes, ejes extrafuertes, herramientas, ejes en general, palas de hélices, cubos de ruedas, cigüeñales, bielas, recipientes sometidos a presión, camisas para cilindros, válvulas y algunos elementos estructurales. Esta clase de aceros se trata adecuadamente a fin de obtener el máximo rendimiento de su aleación. Las prácticas de la cementación, de la cianuración, de la nitruración, del temple al agua o al aceite, del recocido y de ia normalización sirven para mejorar las propiedades físicas de los aceros aleados.
Los inoxidables se emplean sobre todo cuando se trata principalmente de vencer la acción de los agentes corrosivos y deslustradores como en el caso de calderas, de tubos para alambiques y serpentines, de equipos para lecherías, refinado de aceite y química industrial, apliques ornamentales y paletas de turbinas.
Propiedades físicas del acero
Una vez fabricado el acero, se pueden alterar sus propiedades físicas por diversos procedimientos, que pueden ser trabajos en frío o en caliente y tratamientos térmicos. El trabajo en caliente por laminación o forja afina la estructura cristalina del acero fundido y aumenta su compactibilidad, resistencia y ductilidad. El laminado o el estirado en frío tensan y comprimen la estructura cristalina; aumentan la resistencia, pero disminuyen la ductilidad.
El tratamiento térmico es una expresión genérica que significa calentar el acero a temperaturas determinadas para obtener las propiedades requeridas. Son muchos los tratamientos térmicos que se utilizan y casi todos se basan en el hecho de que el acero es esencialmente una aleación de hierro y carbono, cuyas características pueden variar según el tratamiento —en caliente o en frío— a que se le someta. Esto es particularmente cierto cuando la temperatura es lo suficientemente elevada para descomponer o alterar los carburos contenidos en el acero. Por tanto, un enfriamiento rápido cuando el metal alcanza temperaturas superiores a la crítica mantiene en solución los carburos de hierro y demás elementos, lo que beneficia su calidad en grado máximo. Este enfriamiento o temple, que puede realizarse al aire, aceite o agua, produce también un estado de deformación que se aminora con el revenido. Los procesos de homogeneización y recocido utilizan el mismo principio, es decir, la solubilidad de los carburos a la temperatura crítica y el ritmo de transformación también crítica del acero. La carburación y nitruración se basan en la teoría de la solubilidad del carbono y del nitrógeno, respectivamente, en el acero. En consecuencia, se pueden añadir dichos elementos a discreción en las zonas expuestas a tratamiento.
Calidad y contraste del acero
Los trabajos de investigación y las necesidades del mercado han originado una gran variedad de aceros. El contraste metalúrgico de la producción de acero ha avanzado progresivamente. Al principio, el punto más interesante era la comprobación química de la composición. Después se comenzó a considerar el tamaño del grano y su repercusión en las propiedades del acero, así como su resistencia a la torsión, tracción y choques, su dureza, temple, solidez interna y estructura microscópica.
El tamaño del grano, la composición química, el sistema de fusión y el efecto producido por los elementos de aleación son los factores principales que deciden las propiedades definitivas. Los aceros se producen de acuerdo con grados específicos de temple, normas de pureza y propiedades físicas antes y después del tratamiento térmico prescrito. Se podría decir que los aceros se fabrican hoy «a la medida».
Economía del acero
Cuando la industrialización alcanzó su mayoría de edad, el acero se convirtió no sólo en el producto más importante, sino también en el más valioso del presupuesto económico. En Norteamérica actúa como barómetro de la economía nacional, relacionado como está con la industria transformadora. Lo dicho se aplica asimismo al mercado internacional. Es un axioma económico que la nación de mayor producción de acero se convierte, por tal motivo, en el árbitro de la economía mundial.
En el periodo anterior a 1890, la Gran Bretaña era la mayor productora de hierro en el mundo y su economía como nación y corazón del Imperio Británico se basaba sólidamente en esta industria, así como en la del carbón y en la textil. Puede decirse que el advenimiento de la era de los rascacielos en Estados Unidos inclinó la balanza del lado norteamericano. Hasta entonces, la demanda más importante de hierro procedía de los ferrocarriles para el material móvil y vías. La producción de barra comercial, que era el producto principal de los trenes de laminación en su tiempo, disminuyó a medida que comenzó a producirse hierro para la construcción y para la armazón de fábricas y oficinas, así como para la instalación de tuberías que son las arterias de la industria y saneamiento municipales.
Con la introducción de los métodos Bessemer y de solera para la obtención del acero, la era del hierro se convirtió en la del acero y, a pesar de los avances contemporáneos de Gran Bretaña, Alemania y Francia, la corriente de producción se orientó irremisiblemente hacia los Estados Unidos y posteriormente, dentro de niveles más limitados, hacia el Canadá. El acero era imprescindible para la naciente industria del automóvil y para las necesidades de la Armada y de la Marina mercante, todas ellas en pleno desarrollo, y para otras muchas aplicaciones industriales. Los métodos modernos de manufactura lo hicieron más económico que el hierro forjado y que el acero empleado tradicionalmente en la cuchillería y herramientas de corte. Era acero suave, bajo en carbono, pero de gran resistencia a la tracción y dureza.
os viejos hornos de pudelar y los antiguos trenes de laminación cedieron paso a los altos hornos que, irguiendo al cielo su gigantesca masa convertían en pigmeos a los hombres que los atendían. En lugar de laminación mediante un rodillo único, la producción en masa creó los trenes laminadores cuya longitud alcanza centenares de metros. Un tocho de 8 t puede convertirse, en una sola operación, en una banda de acero de longitud y anchura enormes. En las plantas fabriles, las grúas gigantes izan las locomotoras más pesadas y las colocan en barcazas para su embarque transoceánico. La manipulación de mineral fue acelerada por el empleo de vagonetas de volquete y también con la estiba directa al casco de los barcos, gracias a los vertedores de gravedad; lo mismo puede decirse de la descarga que se hacía con cintas transportadoras de cadena, con las que es posible descargar un buque de 10000 t en menos de medio día.
El acero en Norteamérica
A pesar de las cantidades astronómicas que proporcionan los depósitos nativos (Pittsburgh, zona de la máxima importancia por la accesibilidad de la materia prima; Pensilvania, la segunda en producción de mineral; la inmensamente rica Vermilion Range y Mesabi (Minnesota), inaccesible hasta 1875; las minas de Michigan y Wisconsin, responsables de casi todo el mineral producido antes de 1890; el distrito de Alabama-Tennessee, cuyo mineral no se adapta al proceso Bessemer), Norteamérica importa mineral de hierro de España, Cuba y Suecia; este último es de calidad inmejorable.
El manganeso, elemento primordial para la obtención de aceros de esta aleación, se importa de Rusia y la India para hacer frente al aumento de consumo de aleaciones duras. Los yacimientos riquísimos de la zona de Ontario han independizado al Canadá de la importación extranjera. En Estados Unidos, las mejoras tecnológicas redujeron los costes y a medida que se fue haciendo posible el empleo de minerales ricos en fósforo mediante el proceso de solera abierta, se fue dislocando la situación geográfica de las acerías, que antes se agrupaban en las zonas metalíferas en explotación. La industria se desplazó hacia el O favorecida por la implantación de maquinaria moderna que ahorraba mucha mano de obra, con lo que se alteró el sistema seguido de antiguo en la fijación de precios.
Ya antes de la II Guerra Mundial se hizo evidente que las reservas de los yacimientos de la cadena montañosa de Mesabi (Minnesota), disminuían a ritmo alarmante y las cantidades ingentes extraídas durante la guerra hicieron prever su agotamiento en un futuro próximo. Se adoptaron, por tanto, las medidas siguientes para asegurar el abastecimiento continuo de las acerías estadounidenses:
a) la explotación de TaconitA, mineral férrico de grado pobre procedente del Lago Superior;
b) la prospección de yacimientos en el extranjero.
En 1947 fue hallado uno de los más importantes yacimientos en Venezuela, el de Cerro Bolívar, «la montaña de hierro más grande y rica del mundo», aunque la U.S. Steel Corporation no hizo público su descubrimiento hasta 1950. «Little Steel» (Acerías Pequeñas) es el nombre conjunto de marca de fábrica que incluye el grupo de empresas de Bethlehem, Republic, Inland, Youngstown Steel y Tube, aunque el título no resulte muy exacto, puesto que su producción total sólo es superada por la U.S. Steel Corporation.
El acero en España
Ya los romanos tuvieron en gran estima el acero fabricado en España y más tarde, durante la dominación musulmana existía una industria relativamente importante. Con la aplicación del fuelle al procedimiento imperfecto primitivo se consiguió mejorar la calidad y así durante siglos fue famosa la llamada forja catalana, usada en España, Portugal, sur de Francia y en algunas otras regiones. De todos modos, la verdadera industria siderúrgica española no se inicia hasta en la segunda mitad del siglo xviii con la construcción de dos altos hornos en Trubia (Asturias) y otros dos en Málaga. Pronto se desplazó a Vizcaya el centro de gravedad de esta industria, ya que la provincia no sólo contaba con importantes yacimientos ferríferos, sino que los barcos que exportaban el mineral a Inglaterra regresaban cargados de carbón para no realizar la vuelta en lastre. En estas condiciones se creó en 1841 en Bolueta (Bilbao) la Sociedad «Santa Ana», primera empresa siderúrgica vizcaína. A fines del citado año funcionaban en España nueve hornos para acero.
El carbón de Asturias también atrajo al hierro vasco y en 1859 se construyó el primer alto horno de La Felguera. En 1892 se creó la C. A. Basconia; en 1899 la «Nueva Montaña», de Santander; en 1917 la Compañía Siderúrgica del Mediterráneo, de Sagunto; y en 1920 la S. A. Echevarría (fundada hacia 1875) inicia la fabricación de aleaciones de acero. En 1902 se fusionan las sociedades Altos Hornos y Fábricas de Hierro y Acero de Bilbao y Construcciones Vizcaya y la empresa siderúrgica Iberia, de cuya unión surgió la S. A. Altos Hornos de Vizcaya.
Autor: Leandro Alegsa
Diccionarios relacionados
Compartir la definición, preguntar y buscar
Usa la inteligencia artificial para resolver tus dudas
Fuentes bibliográficas y más información de Acero:
[ Más ejemplos de oraciones y usos de "Acero" ]
[ Imágenes relacionadas a "Acero" ]
[ Usos en libros de "Acero" ]
[ Imágenes relacionadas a "Acero" ]
[ Usos en libros de "Acero" ]
Análisis de Acero
Cantidad de letras, vocales y consonantes de Acero
Palabra inversa: orecANúmero de letras: 5
Posee un total de 3 vocales: A e o
Y un total de 2 consonantes: c r
¿Es aceptada "Acero" en el diccionario de la RAE?
Ver si existe en el diccionario RAE: Acero (RAE)Categorías donde se encuentra: Acero
Tecnología
Palabras cercanas
|
Abreviaturas empleadas en la definición
A. = alemán o antes
Más abreviaturas...
Más abreviaturas...
Cómo citar la definición de Acero
Definiciones-de.com (2020). Definición de Acero - Leandro Alegsa © 02/11/2020 url: https://www.definiciones-de.com/Definicion/de/acero_aleacion_ferrica.php
¿Preguntas sobre el significado de esta palabra?: respondemos aquí
[ Imágenes relacionadas a "Acero" ]
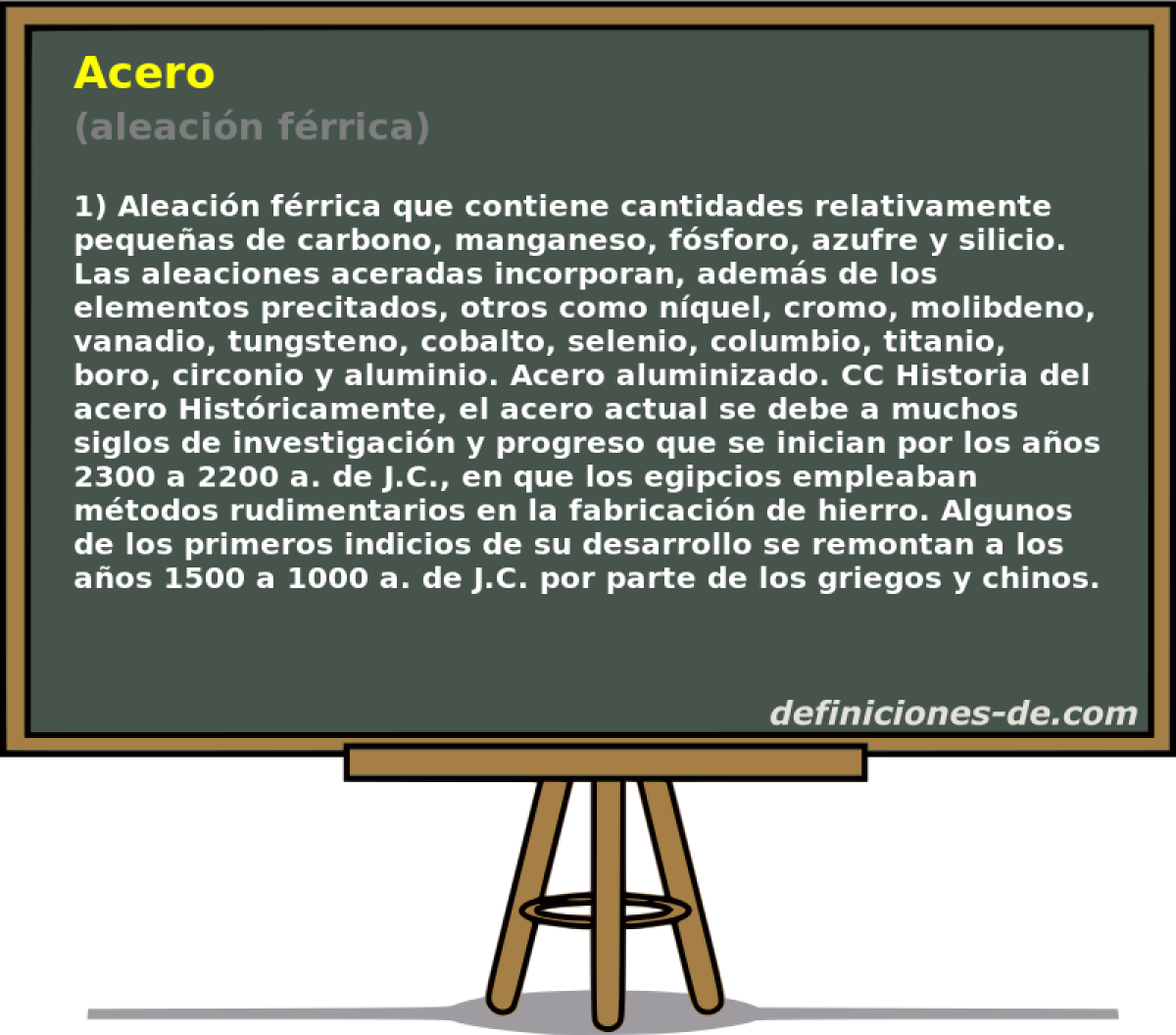
Esta imagen puedes emplearla con fines didácticos en la escuela, institución educativa o proyectos web.
Preguntas y comentarios
No hay ningún comentario todavía